不同原理的流量计,流体温度和压力的变化对测量结果的影响各不相同,因此在测得流体的温度和压力后,要按规定的关系式进行补偿。流体在管道内流动,由于流量传感器、各种阻流件的影响,在管道的不同部位测得的温度和压力值也会有很大差异,因此用作流量测量温度压力补偿的测量点的位置也有明确规定,不能随意确定。
下面以几种典型流量计为例,论述流量测量中温度压力检测点设计中的有关问题。
1供暖流量计温度压力测点的设计
1.1供暖流量计工作原理
在流体流动的管道中设置1个旋涡发生体(阻流件),于是在发生体下游就会交替地产生有规则的旋涡,这种旋涡称为卡曼涡街,该旋涡的频率与流过发生体的流速成正比关系。由于旋涡流量传感器的流通截面积是1个常数,因此旋涡的频率与流过发生体的流体体积流量成正比,如式(1)所示:
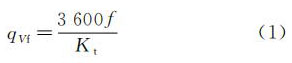
式中:qVf--旋涡发生体出口的工况体积流量,m3/h;f--旋涡频率,P/s;Kt--工作状态下流量系数,1/m3。
1.2温度压力补偿的目的
1.2.1气体流量测量的温度压力补偿
在气体流量测量中,测得工作状态体积流量不是*终目的,得到标准状态体积流量才是*终目标。由工作状态体积流量到标准状态体积流量的换算,一般在流量演算器中完成,其依据如式(2):

式中:qVf--工况条件下的体积流量,m3/h;qVn--标准状态体积流量,m3/h;pf,pn--工作状态、标准状态流体绝对静压,MPa,pn=0.101325MPa;Tf,Tn--工况条件下、标准状态流体热力学温度,K,Tn=293.15K;Zf,Zn--工况条件下、标准状态气体压缩系数。
在式(2)中,Zf和Zn一般由流量演算器按设计好的程序自动计算得到,qVf由式(1)计算得到,而pf和Tf则必须经实测得到。
1.2.2蒸汽流量测量的温度压力补偿
在蒸汽流量测量中,虽然也有温度压力补偿,但补偿的意义与式(2)完全不同。用供暖流量计测量蒸汽流量的系统中,测量的目的是得到蒸汽质量流量值,如式(3)所示:

式中:qm--质量流量,kg/h;ρf--工况条件下的旋涡发生体出口蒸汽密度,kg/m3,可通过查蒸汽密度表得到。1)对于过热蒸汽,可由流量演算器按式(4)自动查蒸汽密度表得到:ρf=f(pf,tf)(4)式中:tf--工况条件下的蒸汽温度,℃。
2)对于饱和蒸汽,可由流量演算器按式(5)和式(6)自动查蒸汽密度表得到:
ρf=f(pf)(5)
ρf=f(tf)(6)
由于蒸汽的状态随温度压力参数而变化,因此有些蒸汽流量计安装地点的蒸汽状态难以确定,有时处于过热状态,有时处于饱和状态。白天管道内流速高,处于过热状态;夜间管道内流速低,进入饱和状态。这时,应对其温度压力都进行测量,由流量演算器自动判断,如果处于过热状态,则仪表自动转向根据式(4)查过热蒸汽密度表;如果已进入饱和区间,则仪表自动转向按式(5)查饱和蒸汽密度表。
利用蒸汽的温度压力参数自动判断蒸汽处于过热状态还是饱和状态,原理如图1所示。关键是判断蒸汽的温度压力值是落在临界饱和曲线的下方还是上方,如果落在下方,则为过热状态;如果落在上方,则为饱和状态。
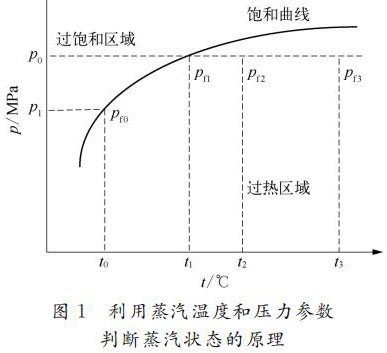
在这种情况下,一般压力测量精确度高,查表得到的密度值的精确度也比较高,因此通常采用式(5)求取密度,式(6)一般不采用。
1.3温度压力测量点位置的选取
气体和蒸汽都是可压缩流体,在流过涡街流量传感器时,都会产生一定的压降。因此,在管道上不同位置开口测流体的绝对静压,得到的结果也不同。在旋涡发生体上游处,静压*高;在旋涡发生体流速*高处,静压*低,再往下游,静压会有少许恢复。
旋涡发生体前后的永久性压降,横河公司提供了计算公式如式(7)所示:△p=1.08ρfv2(7)式中:△p--旋涡发生体前后压降,Pa;v--介质流速,m/s。
以横河公司YF100系列旋涡流量计为例,不同型号流量仪用于温度压力补偿的温度压力测量点的安装位置有不同的要求。压力测点到旋涡发生体的上限距离与下限距离有很大差异。从3.5D~5.5D到3.5D~7.5D,使设计人员犯难,因此研究该距离对仪表的准确安装有重要意义。
仔细研究横河涡街产品的发展历史,在*CD型仪表发展阶段,供暖流量计*小通径只能做到DN25,对于DN25涡街产品,5.5D即为138mm,在法兰下游的管道上开取压口,在工程上还是可行的。但到了*D型仪表发展阶段,*小通径可达到DN15,同样是5.5D,但对应的尺寸变为83mm,要在如此短的距离上开取压口,需要放宽距离以满足工程中的需求。无论哪种情况,实际上两者本质上是一致的。
2差压流量计温度压力测点位置的设计
差压式流量计的种类很多,下面以使用*多的标准差压式流量计为例,说明温度压力测点位置的设计。
2.1差压流量计工作原理
差压流量计工作原理如式(8)所示:

式中:C--流出系数;β--直径比,β=d/D;D--管道内径,m;d--工作条件下节流件的开孔直径,m;ε1--节流件正端取压口平面上的可膨胀性系数;ρ1--节流件正端取压口平面上的流体密度,kg/m3。
差压流量计的本质是质量流量计,在式(8)中,没有出现温度和压力这两个变量,但应用这种流量计测量气体和蒸汽的流量时,流体温度和压力的变化,会使式中的密度ρ1产生变化,进而影响流量示值。
对于组分稳定的气体,可用式(9)计算ρ1:

式中:p1--节流件正端取压口平面上的流体压力,MPa;pn--气体标准状态压力,取值为0.101325MPa;Tf1--节流件正端取压口平面上的流体温度,K;Zf1--工作状态下气体压缩系数,纯数;ρn--标准状态流体密度,kg/m3。
对蒸汽来说,可用式(10)由流量演算器自动查表的方法得到ρ1:
ρ1=f(p1,Tf1)(10)
毫无疑问,式(9)和式(10)都表明,压力取自正端取压口,在具体实施时也比较方便,难的是正端取压口处的流体温度的测量。
文献[6]和文献[7]的相关内容规定:“流体温度*好在一次装置下游测量,测量时需特别小心。温度计套管或插套所占空间应尽可能小,如果插套位于下游,其与一次装置之间的距离至少应为5D,当流体是气体时,*大为15D。如果套管位于上游,则根据一次装置的形式,采用规定的值”。
该标准还规定,一般可以假设差压口上游和下游的流体温度是相同的。然而,如果流体是非理想流体,而又需要计量准确,且上游取压口和一次装置下游测温处又存在较大的压力损失,则假设两点之间是等焓膨胀,必须根据下游温度计算上游温度。对于孔板计算时,应根据下式计算压力损失△ω。
△ω=(1-β1.9)△p (11)
式中:△ω--一次装置压力损失,Pa。
然后,可以采用焦耳-汤姆逊系数μJT(JouleThomsonCoefficient)计算上游取压口到下游测温处的相应温差△T:
△T=μJT△ω(12)
在式(11),(12)中,式(11)是经常用的,使用并不难,而式(12)使用的并不多,原因是μJT求取有难度。
2.2μJT的求取
ISO5167.1-2003的*3.3.4节定义,焦耳-汤姆逊系数又称等焓温度-压力系数,是等焓下相对于压力的温度变化速率:
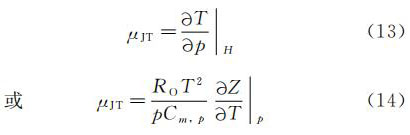
式中:T--绝对(热力学)温度;p--流经管道的流体静压;H--焓;RO--通用气体常数;Cm,p--定压摩尔比热容;Z--压缩系数。
3 涡轮流量计温度压力测点的设计
涡轮流量计用来测量气体流量时,也需要进行温度压力补偿,以便将工作状态下的体积流量换算到标准状态体积流量。
该换算所依据的公式与式(2)相同,但是由于测量原理的不同,测压点的位置有很大的差别。GB/T21391-2008《用气体涡轮流量计测量天然气流量》给出了涡轮流量计在管道上典型的安装图。同时在文字描述中规定,涡轮叶轮处的静压测压口至少要有1个,孔径范围在3~12mm。该标准同时规定,温度传感器应安装在叶轮的下游端,其离叶轮的距离应小于5D,伸入管道公称通径约33%处,但长度不能超过150mm。
4 结束语
1)用来测量气体和蒸汽流量的流量计,除了个别的流量计之外,都需进行流体温度、压力补偿。由于流体种类的不同,补偿的目的也不尽相同;由于温度和压力的变化,对不同原理流量计的影响不相同,因此测温点和测压点位置也有不同的要求,只有合理地确定这些位置,才有可能准确地补偿。
2)供暖流量计用于温度压力补偿的测压口,宜选在旋涡发生体下游的直管段上,应尽可能靠近流量计,但应便于施工和维修(不能选在旋涡体上游的直管段上)。测温口应选在测压口下游150~200mm处。
3)差压流量计用于温度压力补偿的测压点,应选在差压正端取压口处;测温点一般选在差压装置下游5D~15D处,并假设差压口上游和下游的流体温度是相同的。如果是非理想气体,而又需要计量精准,且上游取压口和差压装置下游测温处又存在较大的压力损失,则可采用焦耳-汤姆逊系数计算上游取压口到下游温口处的相应温差△T。
4)基于绝热膨胀等焓变化的原理,利用蒸汽性质表,可方便地求取适用于蒸汽的焦耳-汤姆逊系数。
5)涡轮流量计用于温度压力补偿的测压点,宜设在涡轮叶轮前取压口处;测温口应选在叶轮下游段,离叶轮的距离应小于5D。